Flexographic Printing - What is flexographic printing?
Definition of FLEXOGRAPHIC PRINTING:
A method of printing; this process creates an image through relief printing, using flexible plates to form a raised negative of the image, which is inked and then transferred onto the substrate using pressure. Also known as flexography or “flexo” printing, flexographic printing is a modern form of letterpress printing that uses flexible rubber or photopolymer plates to create a raised image that can be transferred onto a wide variety of materials.
There are three stages to flexographic printing; plate making, mounting, and printing. The image carrier in flexographic printing is a flexible plate (or plates) that is attached to the plate cylinder (which is usually made of steel). There are three ways to produce these plates, with each one requiring a particular material or materials to be used to make the plates. The earliest form of flexographic printing used natural rubbers to make plates, while most modern flexographic printing uses synthetic rubbers. These plates are created using a moulding process; a negative of the image is created on a metal plate (early plates used zinc, before being replaced by magnesium), which is then used to make a mould in plastic or glass, which becomes the master mould for the rubber plate or plates that will be used for printing. More commonly, plates are made using a photopolymer; this is a light sensitive organic substance that undergoes polymerisation when it is exposed to light. To produce a photopolymer plate, a photographic negative of the image being printed is placed over the photopolymeric material (which can be in solid or liquid form) and exposed to UV light. The areas that are exposed (image) undergo polymerisation and harden, while the areas that are covered (non-image) remain soft and soluble; the material is washed and brushed, which removes the soft areas and leaves the negative of the image on the plate in raised form. Finally, some flexographic printers use design rolls (which aren’t, strictly speaking, plates but they do perform the same function – carrying the image – as rubber and photopolymer plates do); a layer of vulcanised rubber is applied to the plate cylinder and a negative of the image is created using a laser, which removes the non-image portions of the rubber surface. This is known as digital platemaking and is usually used to print a continuous pattern or design because the roll doesn’t leave a seam as individual plates do. Where rubber or photopolymer plates are used, the second stage of printing involves mounting the plate (or plates) onto the plate cylinder (or cylinders), usually by means of an adhesive backing, before printing can begin.
Flexographic printing can use a variety of inks, although they do tend to be volatile, quick drying liquid inks; they dry through evaporation of the vehicle and are well suited to high volume, high speed printing, which requires quick drying inks to avoid smudging. Ink is usually transferred from an ink fountain in one of two ways; a fountain roller can transfer ink from the fountain to the anilox roll or the anilox roll can pass through the ink fountain itself, with any excess ink being removed by a doctor blade that passes across the anilox roll. The anilox roll is made of an engraved metal or ceramic and its surface has hundreds or thousands of cells per inch; ink collects in the cells with either the fountain roller or doctor blade controlling the transfer of ink to reduce printing defects such as pinholing. A doctor blade is usually chosen over a fountain roller when there is a requirement for high speed printing. The anilox roll then deposits ink onto the plate cylinder, with the raised areas (image) being inked while the recess areas (non-image) remain clear. The substrate is then fed between the plate cylinder and an impression cylinder (usually made of steel), which uses pressure to transfer the ink (and therefore the image) onto the substrate; the use of a plate cylinder (or image cylinder) and an impression cylinder means that flexographic printing is a form of rotary printing (and requires a rotary printing press). While this process tends to use quick drying inks anyway, UV inks can also be used to further speed up the drying process and prevent smudging.
This method of printing is capable of full colour prints; each colour requires its own colour station and flexographic presses can have between two to eight colour stations (although they usually have six), each of which has its own ink fountain, fountain roller, plate cylinder (and plate), and impression cylinder. These colour stations can be arranged in three different ways; a stack press stacks the stations vertically (making them easy to access and allowing both sides of a substrate to be printed); a central impression press arranges the stations in a circle around the impression cylinder (producing high quality print but only on one side of the substrate); and an in-line press places the stations horizontally (allowing thicker substrates to be printed on and, if a turnbar is used, allowing both sides to be printed). Great care needs to be taken when printing multiple colours because, if any of the different plates are misaligned, the colours won’t align correctly to form the final image.
Flexographic printing has undergone a number of developments that have brought it a long way from the earliest presses that were first used in the late 19th century; the 20th century saw great a number of advances in the production of printing presses, printing inks, and printing plates (and the materials they could be made from). It is a web fed process (it isn’t suitable for individual sheets) and, due to its use of flexible plates and its ability to print using a variety of inks, it is capable of printing onto a large range of materials including plastics, foils and metallic films, acetate film, cellophane, paper, polyester, polyethylene, polypropylene, polystyrene, vinyl, and latex (some of which other printing processes cannot print on well or at all). This makes flexographic printing a popular process for printing items such as packaging, corrugated boxes, shopping bags, food packaging, drink cartons, disposable cups and containers, wallpapers, newspapers, envelopes, and labels. Its use of fast drying inks allows printing to be done much more quickly, which reduces overall production costs and makes flexographic printing ideal for high volume printing. It is also capable (with some care) of producing high quality print that comes close to the print quality of lithographic printing, although it can usually be distinguished from other forms of printing by a slight halo effect around the outline(s) of the printed image.
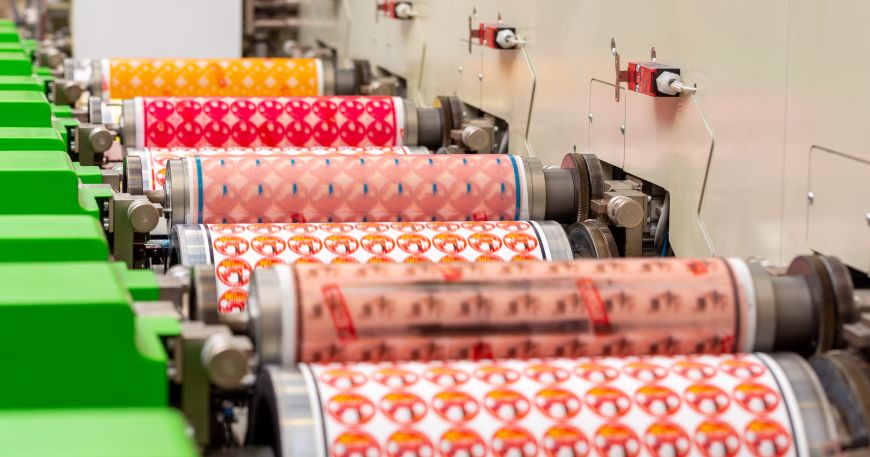
Here is the Harvard-style citation to use if you would like to reference this definition of the term flexographic printing:
Label Planet (2016) What is flexographic printing? | Flexographic Printing Definition. Available at: https://www.labelplanet.co.uk/glossary/flexographic-printing/ (Accessed: January 1, 2024).
Related Questions