Lithographic Printing - What is lithographic printing?
Definition of LITHOGRAPHIC PRINTING:
A method of printing; this process creates an image through planographic printing, using an aluminium plate coated with water and ink to carry both the image and non-image areas of an image, before the ink (and therefore the image) is transferred onto the substrate using pressure. Planographic printing refers to printing methods in which the image and non-image areas exist together on a flat plate, as opposed to raised or relief printing in which the different areas sit on two distinct layers.
Lithographic printing (also known as lithography or “litho”) is based on the principle that oil and water do not (easily) mix; during the printing process, the plate is treated so that the image areas will be receptive to oil/repel water, the non-image areas will be receptive to water/repel oil, and the two areas will remain separate due to the natural repulsion between oil and water.
Traditional lithographic printing used a stone plate (made of limestone) as the image carrier, with the name “lithography” being derived from the Greek for “to write” (graphein) and “stone” (lithos). The process was first discovered in 1796 and involved drawing an image onto the stone plate with oil, fat, or wax; the stone was then treated with a mix of acid and gum arabic to create a layer on the non-image areas of the stone that was hydrophilic (receptive to water). Water would be added to the stone and would be attracted to the non-image areas of the stone and repelled by the oil-based image areas; when the oil-based printing ink was added, it would be repelled by the water in the non-image areas and accepted by the oil-based image areas. The ink would then be transferred to a substrate using pressure.
In modern lithographic printing, printing plates are usually made of aluminium (they may also be made from zinc, polyester, mylar or paper) that is coated with a photosensitive emulsion. A negative of the image is created on the plate using analogue or digital methods; in the former, a photographic negative of the image is placed over the emulsion and the plate is exposed to UV light (the image areas undergo polymerisation and harden, while the non-image areas are protected from the UV light and remain soft and soluble, allowing them to be removed), while in the latter, a computer directs a laser across the plate to remove the non-image areas as needed. The non-image areas may also be further treated to enhance their water receptivity (and therefore their ink repellency) using a solution of a gum compound (such as gum arabic) in a process known as desensitisation.
The plate is then attached to the metal plate cylinder on the printing press, where it is coated with water and oil-based printing inks. The “water” is actually a water-based mixture known as a “fountain solution”; the exact contents depend on the type of printing ink being used, but will include water, an acid, a gum (natural or synthetic, to ensure the non-image areas remain desensitised), a corrosion inhibitor (to protect the printing plate), an alcohol-based wetting agent (to increase the viscosity of the solution and improve flow), a fungicide (to prevent any organic growth within the dampening system), an anti foaming agent (to prevent the solution from foaming or bubbling during the printing process), and a drying stimulator (to help the printing ink to dry more efficiently). The fountain solution is stored in a fountain pan and is distributed by the dampening system.
There are two types of dampening systems in use, known as intermittent flow (also known as conventional flow) and continuous flow. In an intermittent system, the fountain solution is picked up by a fountain pan roller, transferred to a ductor roller, which moves between the fountain pan roller and an oscillator roller, which transfers the solution onto the form roller(s). In direct intermittent systems, the form rollers then distribute the solution directly onto the printing plate, while in an indirect (or integrated) intermittent system, the form rollers distribute the solution into the inking system (so that the printing ink and fountain solution are applied to the printing plate simultaneously). The rollers are plated with chrome or aluminium, with the ductor and form rollers sometimes being covered in fabric to increase the amount of solution they can transfer. The flow of fountain solution is controlled by the rate at which the ductor roller moves between the fountain pan and oscillator rollers (which is where the name “intermittent” comes from). In continuous systems, the fountain solution is transferred onto a rubber covered metering roller (either by a fountain pan roller or by the metering roller itself), then onto a transfer roller, which distributes the solution onto the form roller(s). In an inker feed continuous system, the solution is then distributed into the inking system, while a plate feed distributes the solution onto the plate directly. The inking system transfers the printing ink from the ink fountain to the printing plate, and includes a number of different rollers that decrease the viscosity of the ink to improve its flow and ensure a better quality of print.
Lithographic printing uses thick paste inks that are highly viscous; these inks are made using a pigment and an oil-based vehicle, which allows the ink to be positioned correctly (in the oil receptive image areas) and to dry quickly through a combination of absorption, oxidation, and polymerisation.
The process creates a pattern of areas whereby the image areas are both olephilic (oil receptive) and hydrophobic (water repellent) and the non-image areas are both olephobic (oil repellent) and hydrophilic (water receptive). The water-based fountain solution is attracted to the non-image areas (and repelled by the image areas), while the oil-based printing ink is attracted to the image areas (and repelled by the non-image areas), and the two are kept separate by their natural repulsion. The substrate is then passed between the plate cylinder and a metal impression cylinder, which transfers the ink (and therefore the image) onto the substrate using pressure. Lithographic printing is quite flexible in that it is able to process substrates in web and sheet form (web fed and sheet fed respectively), can print both sides of a web or sheet simultaneously (known as “perfecting”), and can print in colour (with each colour having its own printing unit and printing plate (these are lined up in series), although great care needs to be taken to ensure that the different plates are aligned perfectly), including full colour prints using the four process colour model.
Lithographic printing is capable of printing onto a wide variety of materials, including metals, foils, and plastics. Where the substrate being used is made of paper, the paper needs to be treated and coated on at least one side (if not both) to improve its surface and internal strength, to increase its ink receptivity, and to increase its water resistance (due to the use of and proximity to the fountain solution in the dampening system). Paper that has been specially treated and prepared for use on a lithographic press is known as lithographic paper (or litho paper).
This process is capable of high speed, high volume printing (particularly on web fed presses), and can maintain a high level of print quality and detail. It has been used to print a variety of items, including maps, books, newspapers and magazines, and various forms of packaging. It has also been used extensively by artists to create original artworks and prints in small volume editions, along with fine art prints, posters, wallpapers, and illustrations in books, newspapers, and magazines.
Today, lithographic printing tends to exist more commonly in the form of offset lithography, which is a direct descendent of lithographic printing. This form of printing involves an additional stage whereby the image is transferred from the plate cylinder to an intermediary blanket cylinder before being transferred to the substrate (which passes between the blanket cylinder and the impression cylinder). This process is one of the most common printing processes used today, particularly for high volume commercial printing tasks such as printing books, newspapers, and packaging. Due to the popularity of offset lithography, the term lithography is often used to refer to offset lithography. In order to make a clear distinction between the two, lithography is sometimes referred to as “direct lithography” to differentiate the process from the more common offset process.
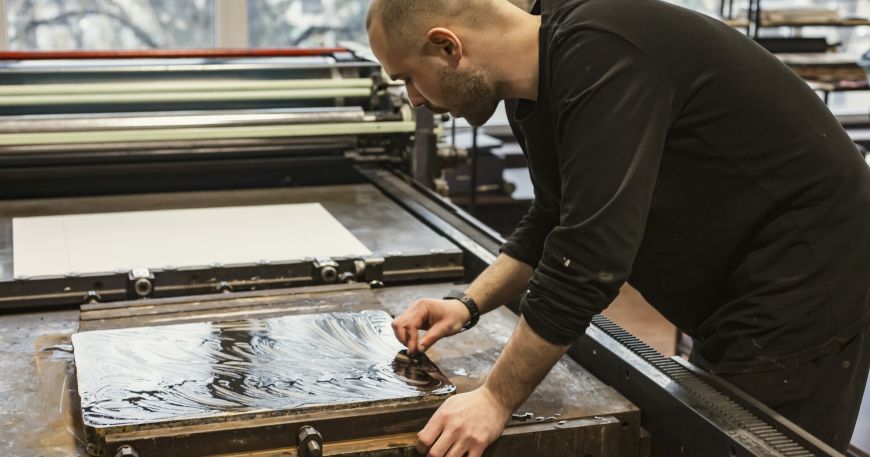
Here is the Harvard-style citation to use if you would like to reference this definition of the term lithographic printing:
Label Planet (2016) What is lithographic printing? | Lithographic Printing Definition. Available at: https://www.labelplanet.co.uk/glossary/lithographic-printing/ (Accessed: January 1, 2024).
Related Questions